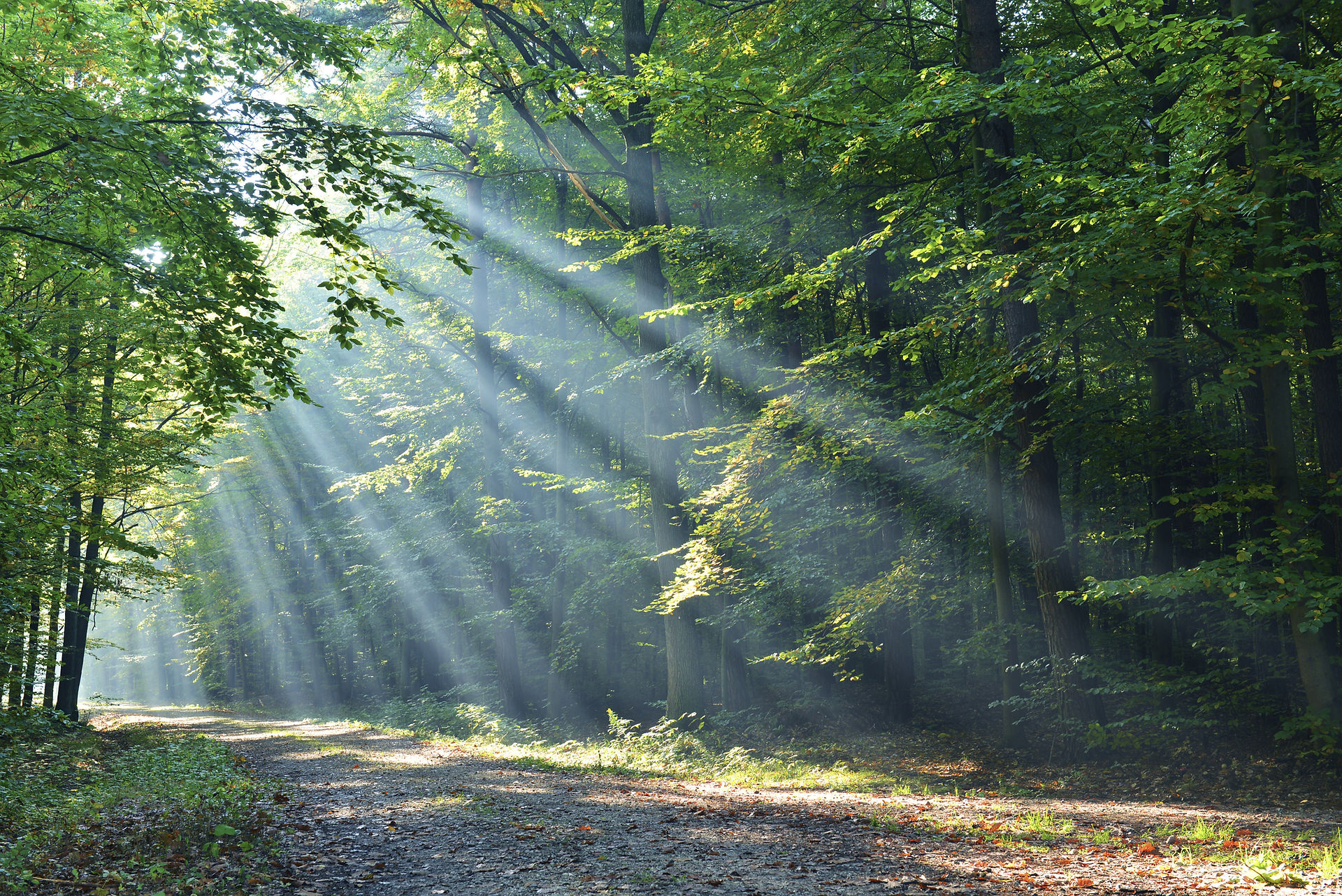

Violin making classes bringing together people who have a passion for stringed instruments and would love to make their own violin, viola or cello in a stress-free, relaxed environment yet producing instruments of high quality.
As there will only be few people per class, students will receive lots of individual attention.
Options: Once or twice a week (each session between 2 and 6 hours) or alternatively the intensive several day in person class from 10.00am to 4.00pm. I am always happy to try and work around your schedule.
These classes are not intended to train professional violin makers, but are aimed at giving hobbyists the opportunity of using a professional workshop under guidance each step of the way. No previous woodworking experience is necessary.
Blog of one of my current students Marcy Luikart
Overview
Special points of interest
You will …..
-
Become part of a community of hundreds of amateur violin makers around the world.
-
Make a violin for your child, friend or yourself.
-
Not only learn an interesting craft, but make an asset with a reasonable resale value, recovering all costs invested.
-
Interact with people from all walks of life sharing a common interest.
All tools will be provided and students will only need to cover actual materials as in wood, varnish, strings, etc.



1. Practice back: Making a practice violin back from locally available maple enables the student to learn the skills of glueing the centre joint, preparing the edge, doing the purfling (inlay), arching (shaping the outside curve), thicknessing (carving out the back) and completing the edge work without endangering an expensive piece of tonewood.
2. Rib structure: Glueing and shaping blocks to the mould, then bending and glueing the ribs (sides) to the blocks and finally putting in the linings.
3. Carving of plates: Using the techniques acquired while making the practice plate, making the back and front plates, but this time working with good-quality tonewood imported from Germany or Italy.
4. F-holes and bass bar: Cutting the f-holes and fitting a bass bar to the completed front plate.
5. Assembling the sound box: Finishing off the inner work on the ribs and then glueing the back and front onto the rib structure. Then completing the edge work and scraping the sound box .
6. Neck and scroll: Shaping and carving the scroll, followed by glueing and working on the fingerboard, and then shaping the neck.
7. Neck joint: Cutting the mortise into the body, then fitting the neck to the body taking into account the neck elevation and alignment. Then comes the final shaping of the neck and the button. The violin is now finished 'in the White' !
8. Primer, sealer and varnish: The varnishing procedure uses materials imported from professional violin varnish makers. My varnish recipe is no secret and if students wish to go ahead and make their own following my instructions that would be fine however from experience it requires a lot of patience and dedication. Varnishing entails coloring the wood, sealing it and applying the color varnish.
9. Setting up: Installing the pegs, nut, saddle, sound post and bridge. Before attempting the final work on the new violin, students will do several practice bridges and sound posts to become familiar with these most important jobs.
10. Achievement: The most rewarding experience hearing your first violin come to life! We will invite a leading violinist to the workshop to play your finished violin to all the other students and have a celebratory party!
The Workshop
Course outline
​
To enroll or for more information please contact brian.lisus@icloud.com or Phone: (805) 403-9475